
LTL proudly possesses over three decades of expertise in manufacturing transformers. At present, we deliver to a vast range of customer requirements across the world while adhering to internationally recognized standards including IEC, ANSI & BS. We have always placed significant priority on the mechanical design and the final finish of our transformers and that they meet the defined dielectric strength, mechanical endurance, dynamic and thermal withstand of winding in the event of short circuits. The calibration and optimization of our transformer designs are done through highly advanced in-house built software. The software was specifically developed by LTL for this purpose with the technical collaboration of experts in the field of transformer manufacturing making it easier and flexible for us to deliver to a diverse range of requirements demanded in the industry.
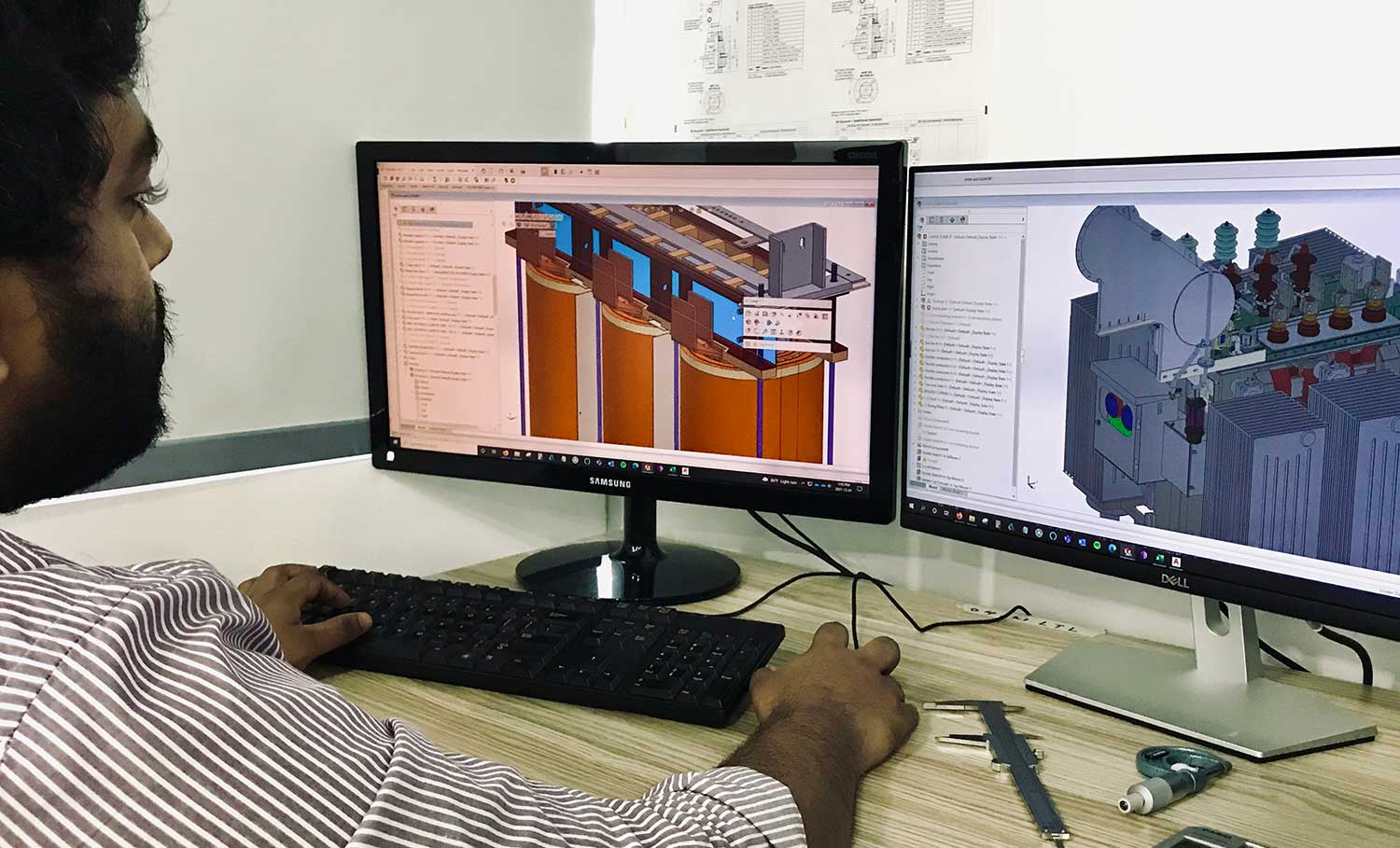
Research and Development

LTL has always been diligent towards incorporating the most advanced and latest technologies in the form of research and development. In our efforts to increase efficiencies and improve environmental standards, we have been constantly investing and developing our products and services to keep the upper hand and better deliver to customers. We take into account a holistic view of the entire life cycle, resulting in the most environmentally friendly products, systems and solutions being used in the production of the transformers. In the latest innovative moves, LTL is committed to starting the manufacturing of transformers incorporating the amorphous core technology, natural ester fluids, and higher thermal insulation-based technologies. Work is already underway to produce a smart distribution transformer incorporating Dynamic Voltage Control to the Future Distribution Transformer. The activities will ultimately help customers across a wide range of sectors to lower their operating costs and emissions. The lower total owning cost will see the customers benefiting with returns over the lifetime of the transformers.

Testing

A new automatic state of the art testing equipment from Phoenix USA has been received at factory. Once this new unit is commissioned, the complete routine testing process will be automated enhancing the efficiency of testing process. Moreover, the testing laboratory of the factory has been relocated inside the premises by adding more space to increase the capacity of the laboratory. The two-story new testing lab, consists of many facilities for customers, including an observation deck, monitoring wide screen, resting room, prayer room and lunchroom.
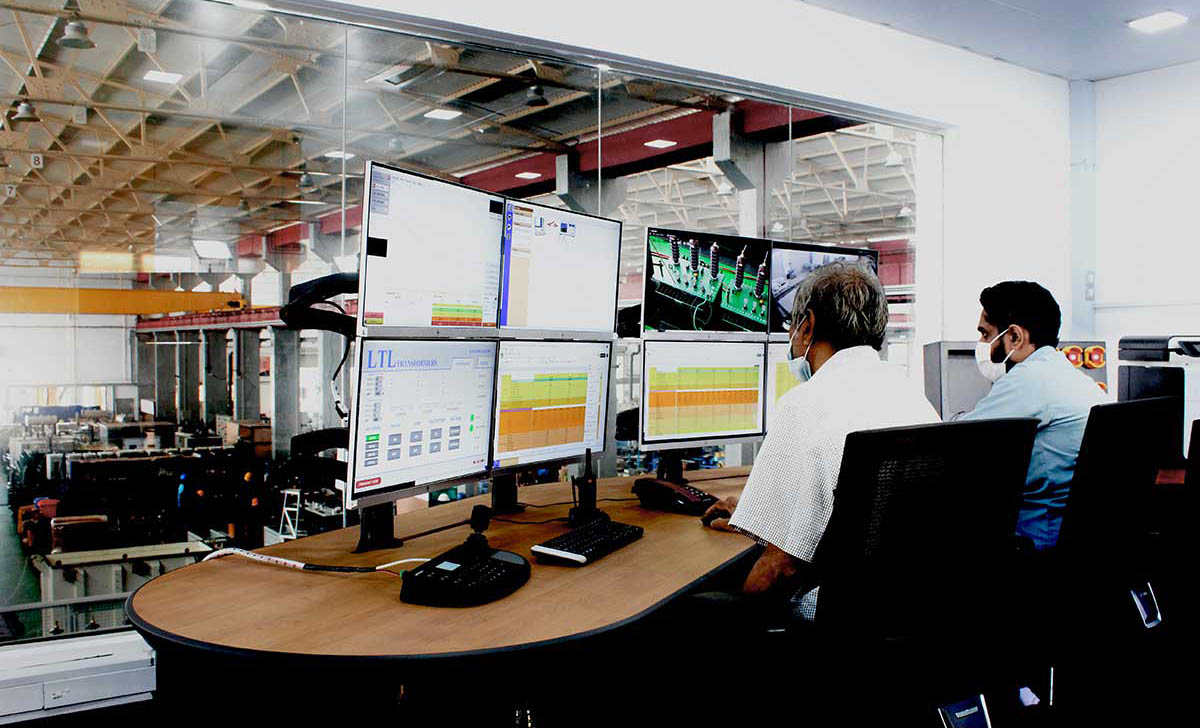
Quality assurance

It is our continuous learning, improvement, innovation, and operational excellence that have led to our reputation of delivering defect free products and services at competitive prices whilst meeting timely delivery standards. In our effort to produce highest quality products and services that meet or possibly exceed what is expected by the customer, we have always has always made it a priority to sustain a quality control and assurance process of the highest standards. All our products are subjected to strict quality criteria through a comprehensive series of mandatory tests to ensure they adhere to the relevant internationally recognized standards such as IEC, ANSI, and BS prior to being dispatched to the customers. Our Integrated Management System conforms to ISO 9001, ISO 14001 & OHSAS 18001 and has been certified by DNVGL of the Netherlands. Furthermore, all our transformers are tested and certified by KEMA Netherlands and CPRI India which are among the most renowned test laboratories for transformers.
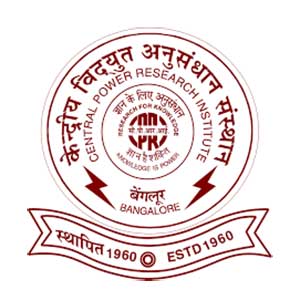
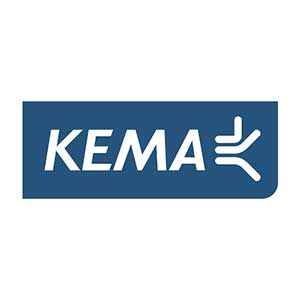
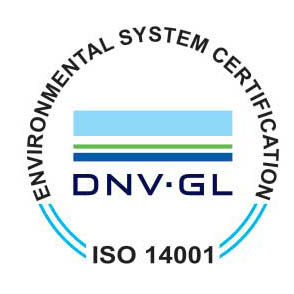
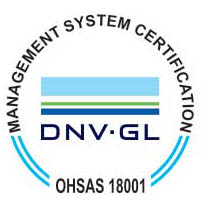
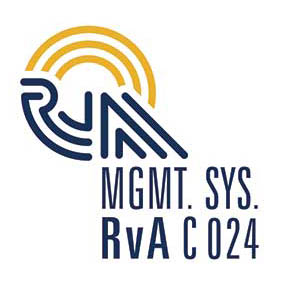
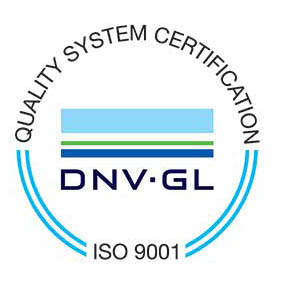
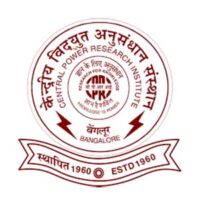
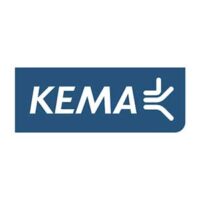
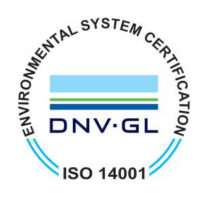
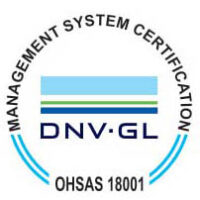
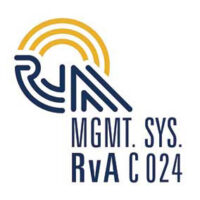
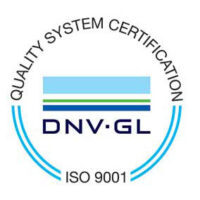
GEORG Core Cutting Machine

The transformer core, which is made from high-quality, cold-rolled grain-oriented silicon steel laminations, belongs to the active part which is generally the most important feature of a transformer. The Automated High-Speed Core Cutting Line from Georg, Germany is another big addition to LTL’s state of the art machinery. This can precisely cut step lap stacked transformer cores. The result is transformers with lower No-load losses, no-load Current and low noise levels. Apart from that, the machine will further enable precision cutting, low burr cutting, minimized scrap, and the highest reliability.
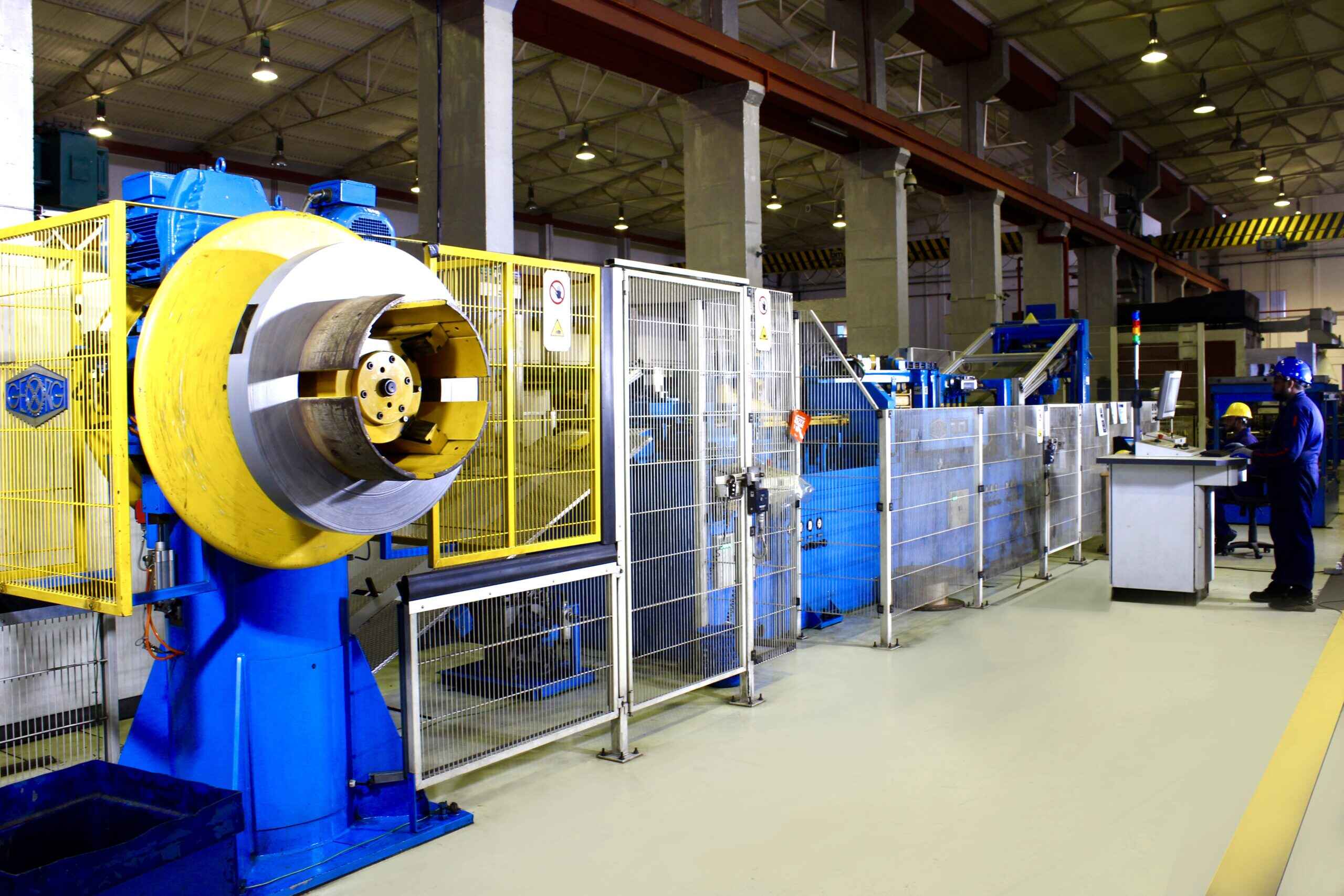
HV Winding Machine (Tuboly)

The production facility of LTL is currently equipped with the newest and most advanced winding machines from world-renowned manufacturers. The high voltage winding machines from Tuboly-Astronic of Switzerland have been installed which significantly increase the production capacity and are instrumental in the timely execution of large contracts while ensuring economical usage of raw material. The HV Winding Machine from Tuboly has further made the entire winding process fully automated improving the consistency of the wound wire and reducing the chances of coil impairment.
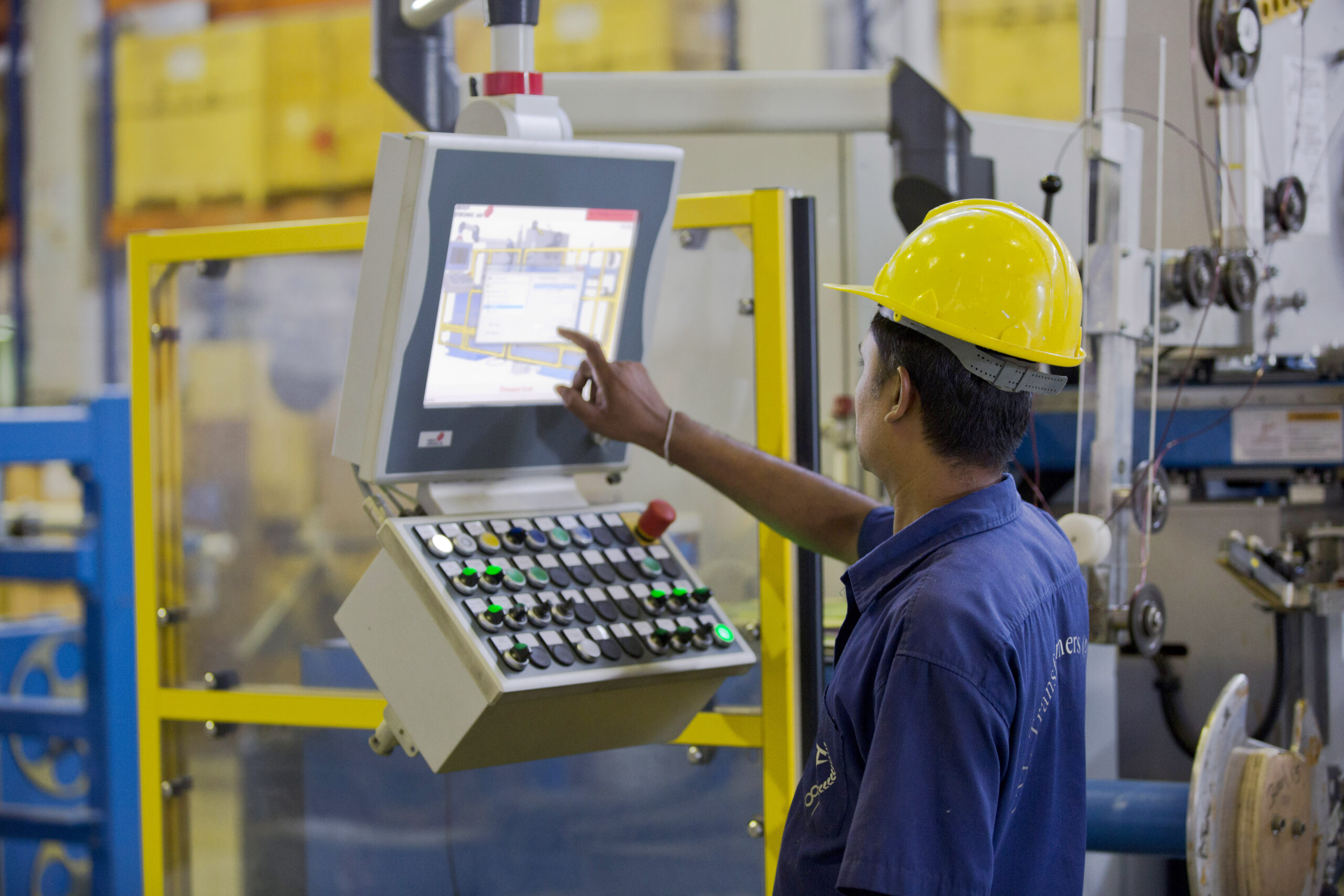
LFH Oven

Low-Frequency Heating (LFH) technology has been identified as a go-to method for the removal of moisture from the cellulose insulation which is a key process in the production of Power and Distribution transformers. The method ensures the trouble-free operation of the transformers for many years to come. In a bid to improve the reliability and life expectancy of LTL’s transformers, Low-Frequency Heating (LFH) technology from Hedrich Germany has been incorporated into the production process. Incidentally, this was the first use of this groundbreaking technology in the entire region. LFH possesses an automatic Oil filling and pressure testing facility that subsequently enhances the efficiency and accuracy of the process drastically.
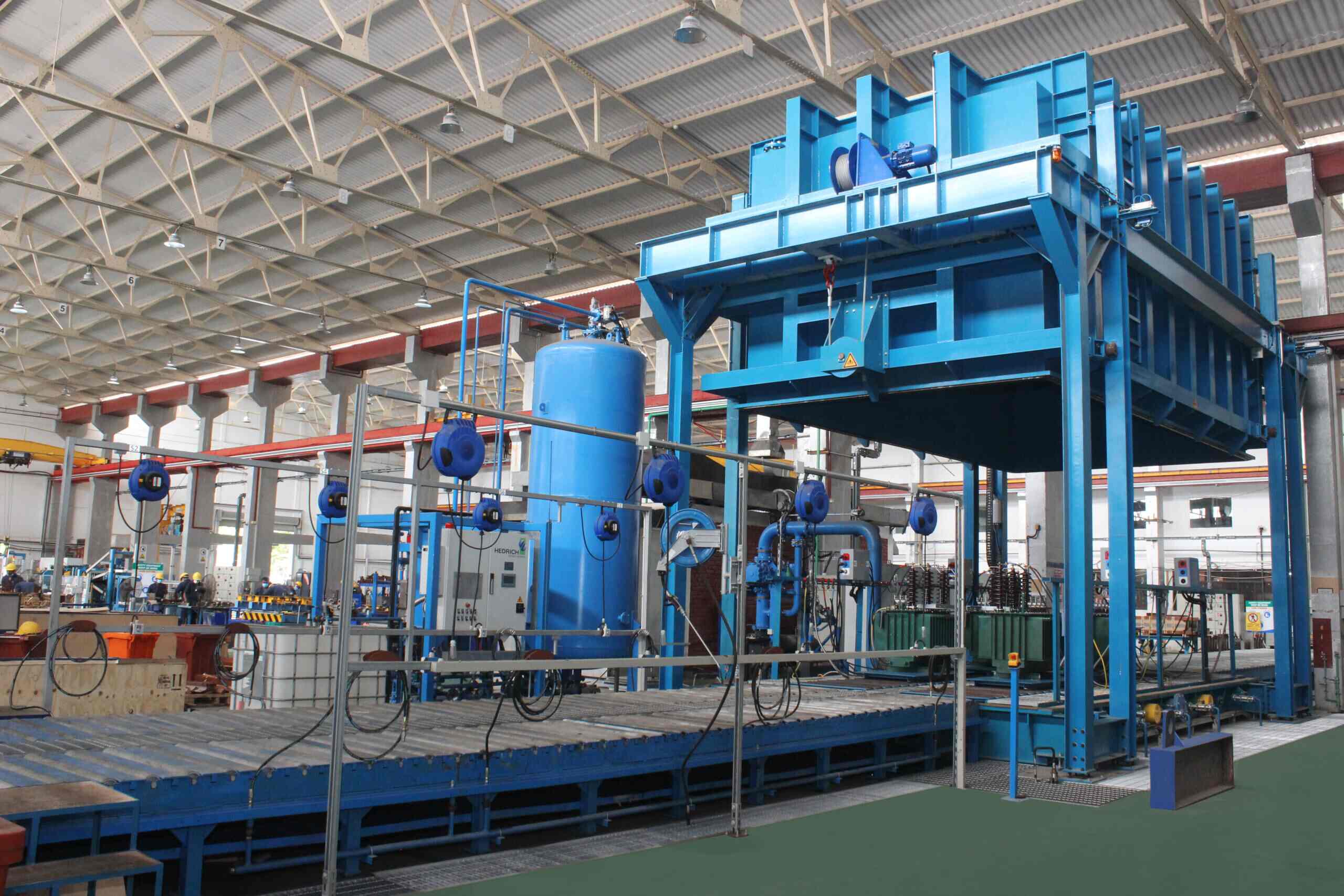